About ActivArmor™
the global leader in 3D printed waterproof cast Alternatives
We leverage revolutionary 3D printing technology to create ActivArmor cast and splints that support patients' active lifestyles.
Follow Us
ABOUT OUR Leadership TEAM
-
A Colorado School of Mines graduate in Chemical Engineering, Diana Hall founded ActivArmor in 2014 while running a mentoring program for children living in poverty.
After working in Fortune 500 companies across the country and finishing her master’s degree in Business from Colorado State University in Fort Collins, Diana moved back to her hometown of Pueblo, CO, to advocate for children on Pueblo’s east side.
Through the mentoring program, Diana worked with children involved in domestic violence situations and living in substandard conditions. The children who wore casts would get them filthy after just weeks of wear from simply playing on the playground or going to school.
“The children with casts for 5 weeks could not even wash their hands to have a snack! One girl had bed bugs in her cast. Another little boy was being raised by his disabled grandparents and was not able to keep his cast dry when showering by himself. He got his cast wet and did not want to get in trouble and had no transportation to get it replaced, so he did not tell and ended up with permanent scarring on his arm from the skin breakdown. That’s when I knew I had to come up with a better solution.”
-
Kris Culbertson is a dynamic Operations & Administrative Executive with a demonstrated history of success in the medical industry. Kris joined ActivArmor following a decade of experience as Chief Neurophysiologist and Sports Medicine Practitioner in his role as President of Elite Neuromonitoring and LifeLAB.
After learning about ActivArmor’s impressive casting solutions, Kris joined the team as the Chief Sales Officer, leading and mentoring ActivArmor’s sales team. Since then, Kris has executed comprehensive sales strategies to drive revenue growth and expand market presence for ActivArmor’s innovative waterproof cast alternatives.
-
Dr. Krystina Vrana is a results-driven accounting and finance leader with over 20 years of experience in financial management, strategic planning, and operational optimization. She holds a Master’s in Accounting, an MBA, and a Doctorate in Finance, equipping her with a deep understanding of financial strategy, corporate governance, and data-driven decision-making.
As the Chief Financial Officer of ActivArmor, Krystina has led a comprehensive overhaul of the company’s financial reporting systems, significantly enhancing transparency and ensuring regulatory compliance across all levels of the organization. Her expertise in financial structuring and process optimization has streamlined operations, improved forecasting accuracy, and strengthened internal controls.
Leveraging her extensive academic background and practical experience, Krystina has also played a key role in refining budgeting processes, optimizing cash flow, and implementing strategic financial initiatives that support ActivArmor’s long-term growth. Her leadership continues to drive financial stability and operational efficiency, positioning the company for sustained success in the medical device industry.
-
Adam Halen has extensive experience as the founder and CEO of Halen Digital Marketing. With over a decade in digital marketing, he specializes in innovative social media strategies and content production.
Adam's expertise has been instrumental in enhancing ActivArmor's online presence and effectively communicating its mission to a broader audience. His strategic insights have positioned ActivArmor as a leader in 3D-printed waterproof cast alternatives.
Beyond his advisory role, Adam is a sought-after speaker and consultant, regularly sharing his knowledge at industry conferences and events.
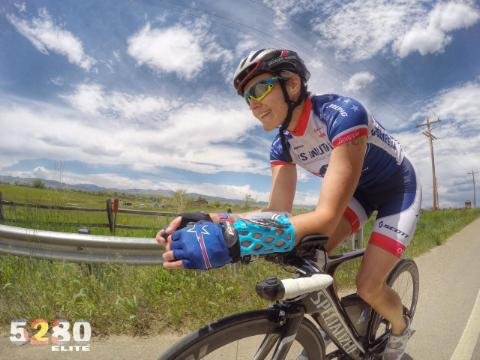
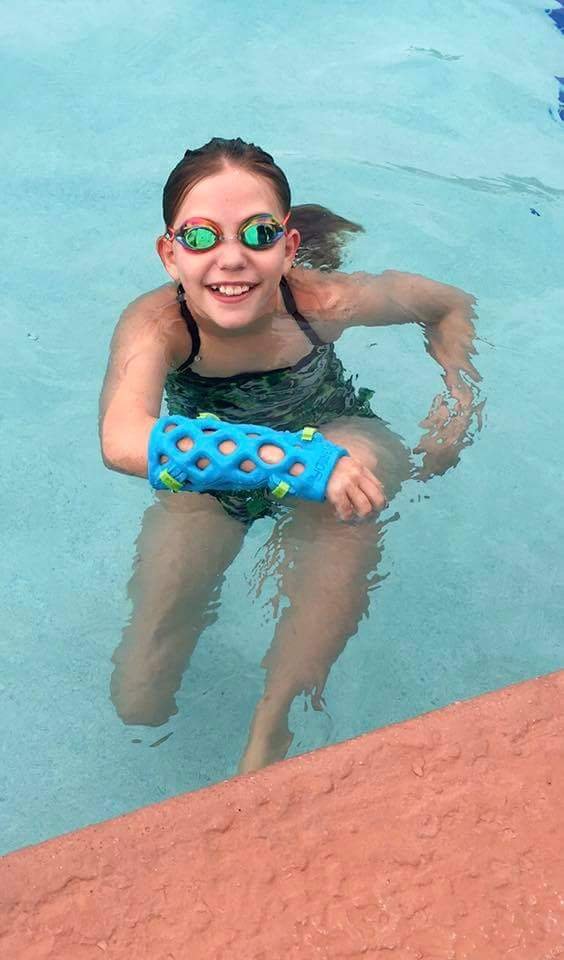

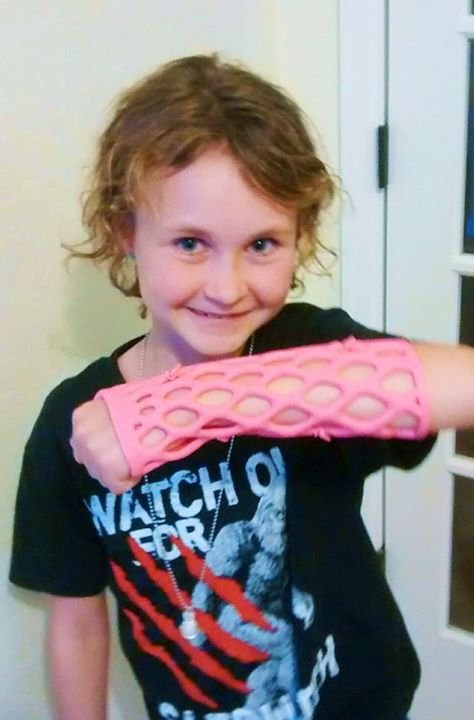
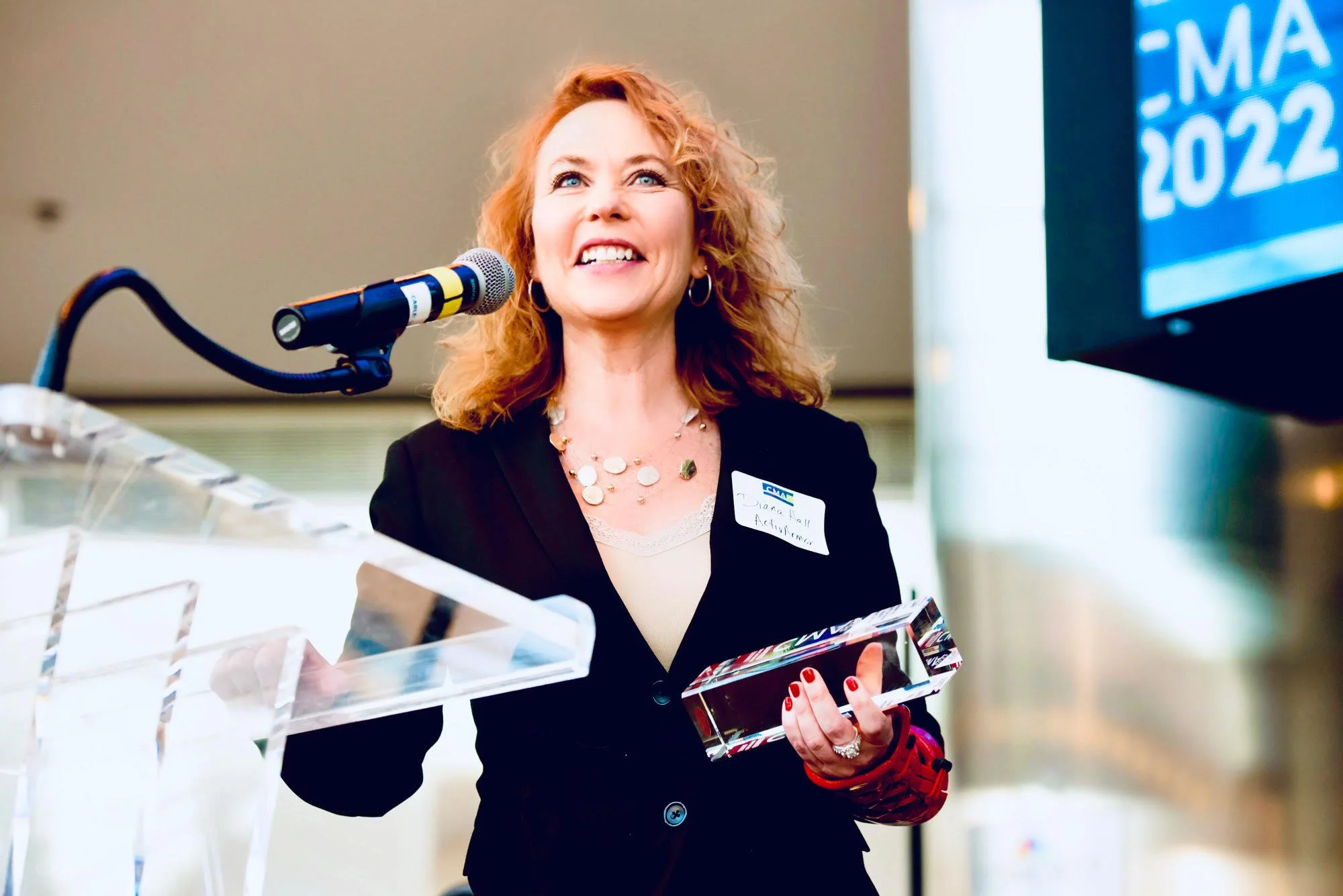
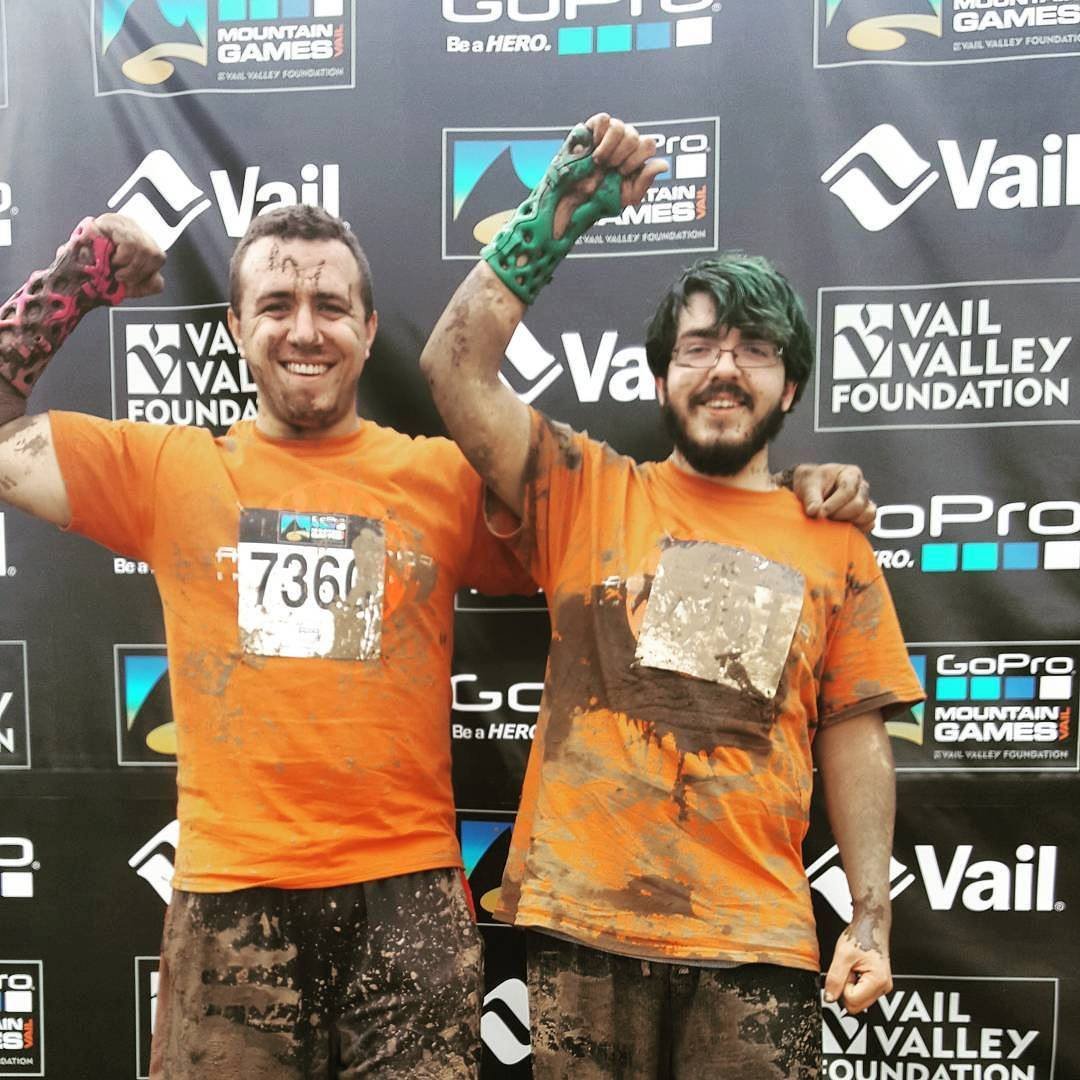
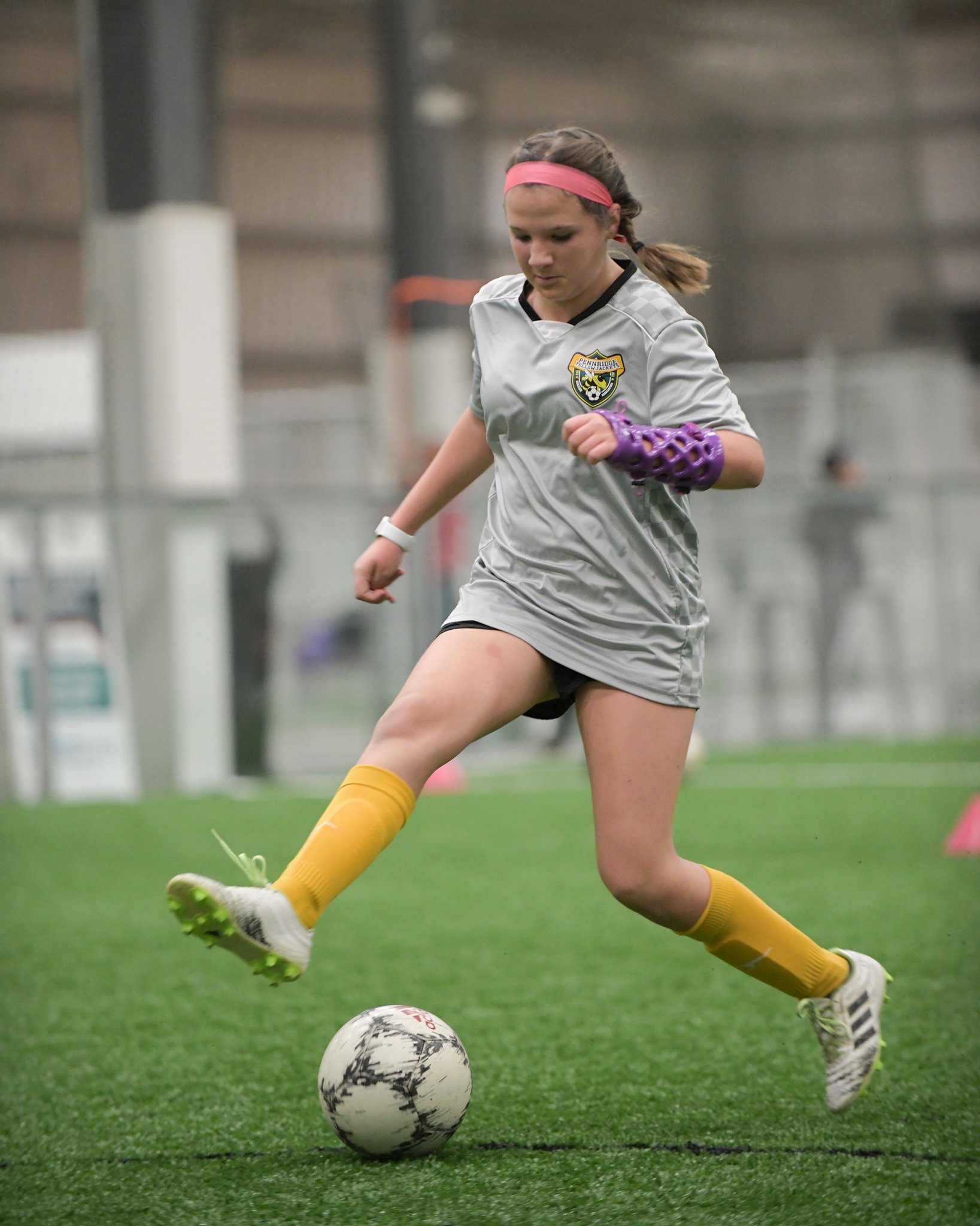
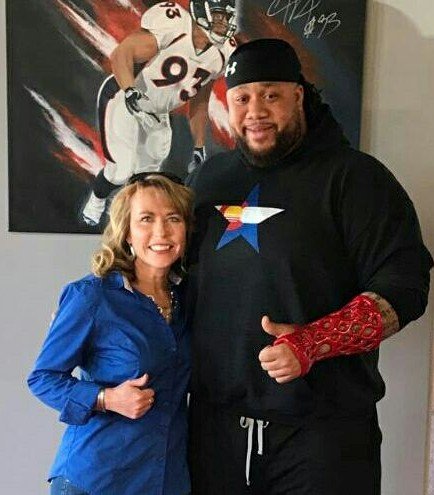
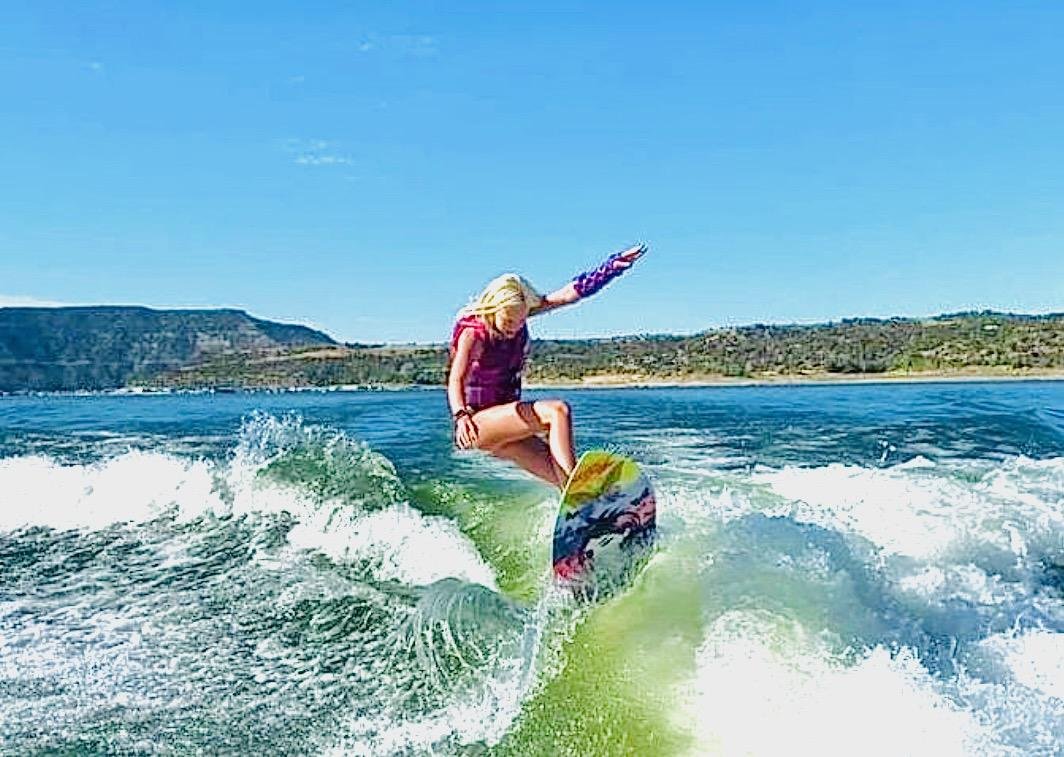

About Our Solution
Diana’s mission was to create a better alternative to casting and splinting by leveraging additive manufacturing.
The goal: Create breathable casts and splints using hygienic materials and a custom-fit design that allows for improved healing, treatment options and the freedom of maintaining an active lifestyle.
The challenge: After researching the current cast options, Diana found that there were many reasons why this technology and product was not available to American consumers.
The solution: ActivArmor’s team of global leaders, engineers, top orthopedic surgeons and sports medicine doctors, regulatory compliance experts, athletes and patients addressed these challenges over 3 years of field tests and hundreds of commercial sales. ActivArmor is now available in clinics across the globe, being worn by professional athletes and patients worldwide.
-
Problem: Design and fabrication of custom splints by hand takes both time and labor.
Solution: Leverage revolutionary 3D technology to produce custom ActivArmor cast and splints
-
Problem: Casts need to be strong enough to heal patient limbs but made with lightweight materials.
Solution: Find the ideal balance of thickness and coverage area (for protection of a broken limb) and lightweight breath-ability (for comfort and freedom for the patient).
-
Problem: Casts need to be durable enough to be used in sports, while still low-profile enough to allow for maximized mobility and freedom of movement.
Solution: Source 100% ABS (Acrylonitrile butadiene styrene) – a stable, hard, and durable plastic used in toys, food packaging, and surgical tools.
-
Problem: Casts need to pass regulations and can’t trap moisture or bacteria against the skin.
Solution: Ensure 3D printed materials and finished products are biocompatible and non-porous.
-
Problem: Casts need to be custom because every patient’s limbs and injuries are unique.
Solution: Implement the right equipment with the right process and quality controls to ensure a precise fit to the limb for accurate immobilization of parts as small as fingers for comfort and ideal healing outcomes.
-
Problem: Casts need to be easily adapted by clinics.
Solution: Implement software that makes it easy for physicians to use.
-
Problem: Casts need to be locked-on like a cast, but also removable like a splint.
Solution: Design cast with strong, locking nylon zip ties with adaptable bungee closure kit, to be applicable for both acute injuries and chronic conditions.
-
Problem: Casts need to be accessible to everyone.
Solution: Make casts available in the same price range as traditional splints, and covered by insurance by developing the latest technology in precision scanning hardware and software affordable, including the labor of CAD design unique to each patient, fabrication and hand-finishing of each device in an FDA-registered manufacturing facility.
About Our Values
Accessibility
Innovation
Sustainability
Empathy